RAWTEK
Shop Representative
Hey, wanted to give you guys a heads up on some prototyping we've been working on lately. We've been working hard on developing a high performance straight through muffler that will perform just as well as big brand names, but offer lower sound levels (who hasn't been pulled over in MTL for a loud exhaust).
Here's a little rundown on how we build our mufflers and I'd love to hear some comments!
The muffler cores are made of T304 stainless steel tube. Our TPM (tube perforating machine) is used to perforate standard stainless steel tubing, instead of the flat punched then rolled and welded construction that most muffler companies like Magnaflow and Borla use. With our TPM machine we eliminate the seam weld on the core, this allows for about 10% more surface area of perforated tube, this means we can build a smaller, lighter muffler with the same sound absorption as a bigger one. We can also vary the amount of perforation per length of tube in order to change the desired sound level.
Here you can see a Rawtek core (top) next to a Magnaflow core (bottom):
Magnaflow core (notice the seam weld):
Rawtek core:
Inside Magnaflow core:
Inside Rawtek core:
The muffler case is made of a flat stainless sheet rolled in house, then is seam welded by our automatic seam welder. Argon is used to assure a perfect weld on both sides of the casing.
Here is a close-up of the seam weld:
Here are all the parts used to assemble:
The core is then spun with stainless steel mesh, and the muffler is very densely packed with the highest quality packing material.
Here is a pic of the final product:
And finally this is a dual in / dual out muffler we built, and installed on a client's car. This particular client noted that our muffler was actually quieter than the factory muffler installed on his car! 89.5db were measured at 5500rpm.
Here's a little rundown on how we build our mufflers and I'd love to hear some comments!
The muffler cores are made of T304 stainless steel tube. Our TPM (tube perforating machine) is used to perforate standard stainless steel tubing, instead of the flat punched then rolled and welded construction that most muffler companies like Magnaflow and Borla use. With our TPM machine we eliminate the seam weld on the core, this allows for about 10% more surface area of perforated tube, this means we can build a smaller, lighter muffler with the same sound absorption as a bigger one. We can also vary the amount of perforation per length of tube in order to change the desired sound level.
Here you can see a Rawtek core (top) next to a Magnaflow core (bottom):
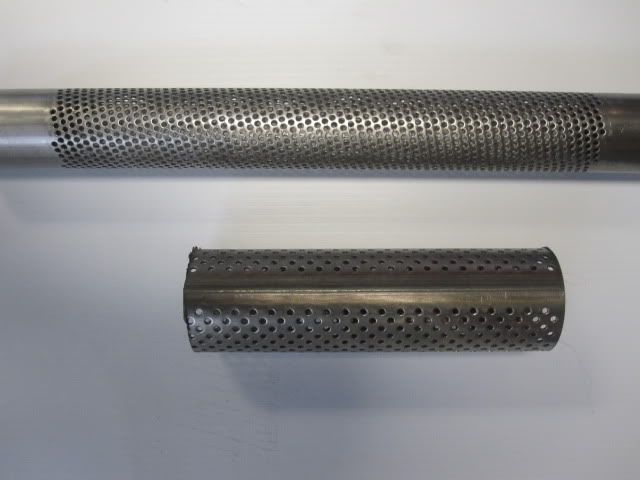
Magnaflow core (notice the seam weld):
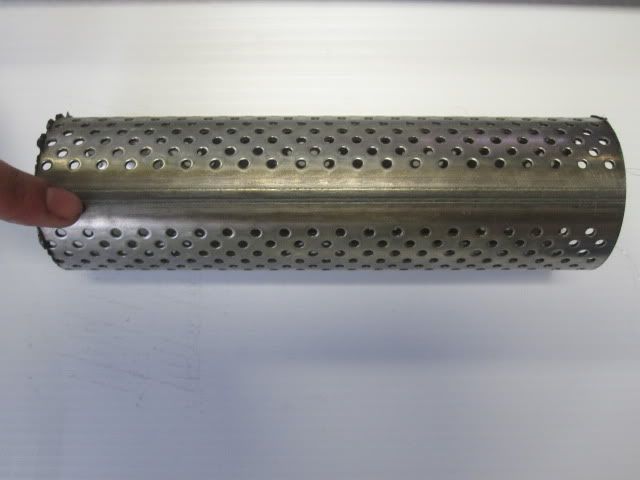
Rawtek core:
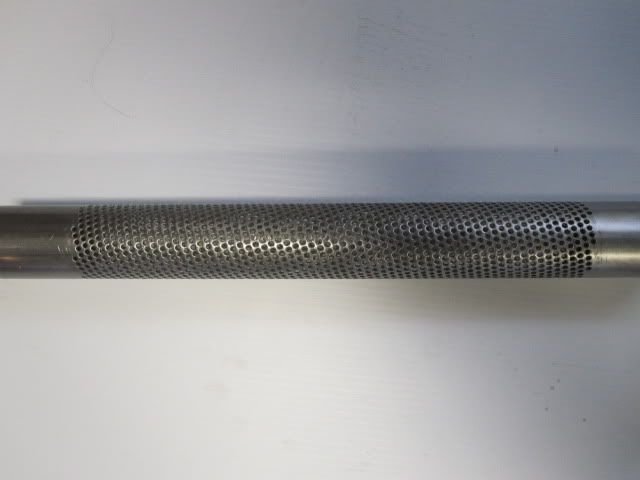
Inside Magnaflow core:
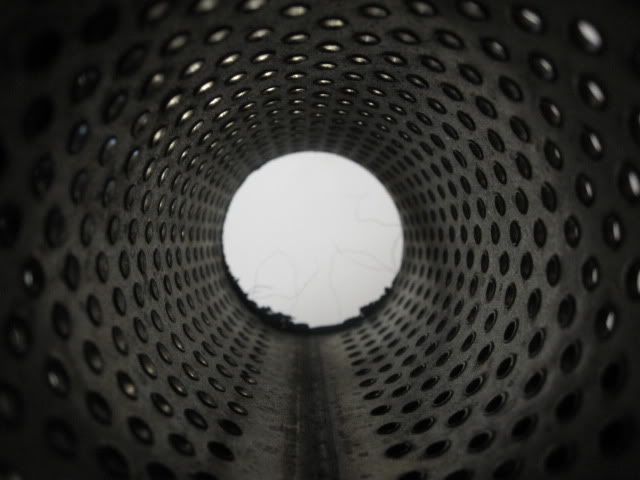
Inside Rawtek core:
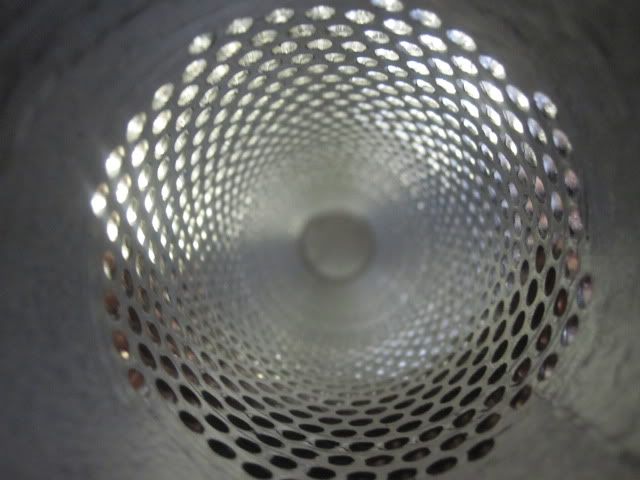
The muffler case is made of a flat stainless sheet rolled in house, then is seam welded by our automatic seam welder. Argon is used to assure a perfect weld on both sides of the casing.
Here is a close-up of the seam weld:
Here are all the parts used to assemble:
The core is then spun with stainless steel mesh, and the muffler is very densely packed with the highest quality packing material.
Here is a pic of the final product:
And finally this is a dual in / dual out muffler we built, and installed on a client's car. This particular client noted that our muffler was actually quieter than the factory muffler installed on his car! 89.5db were measured at 5500rpm.
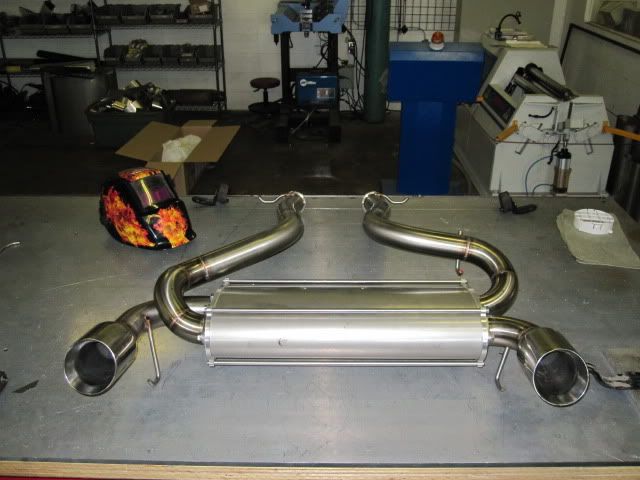
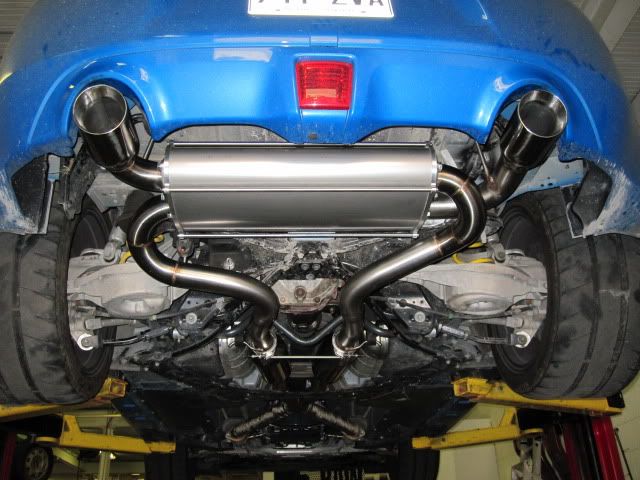
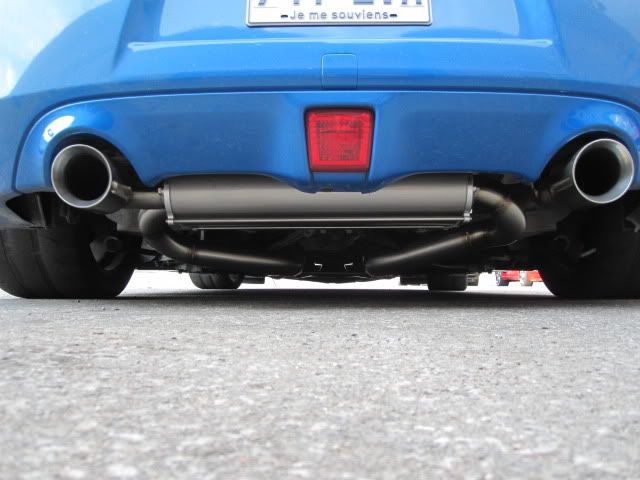
Last edited: